COLLEGE OF ENGINEERING & SCIENCE
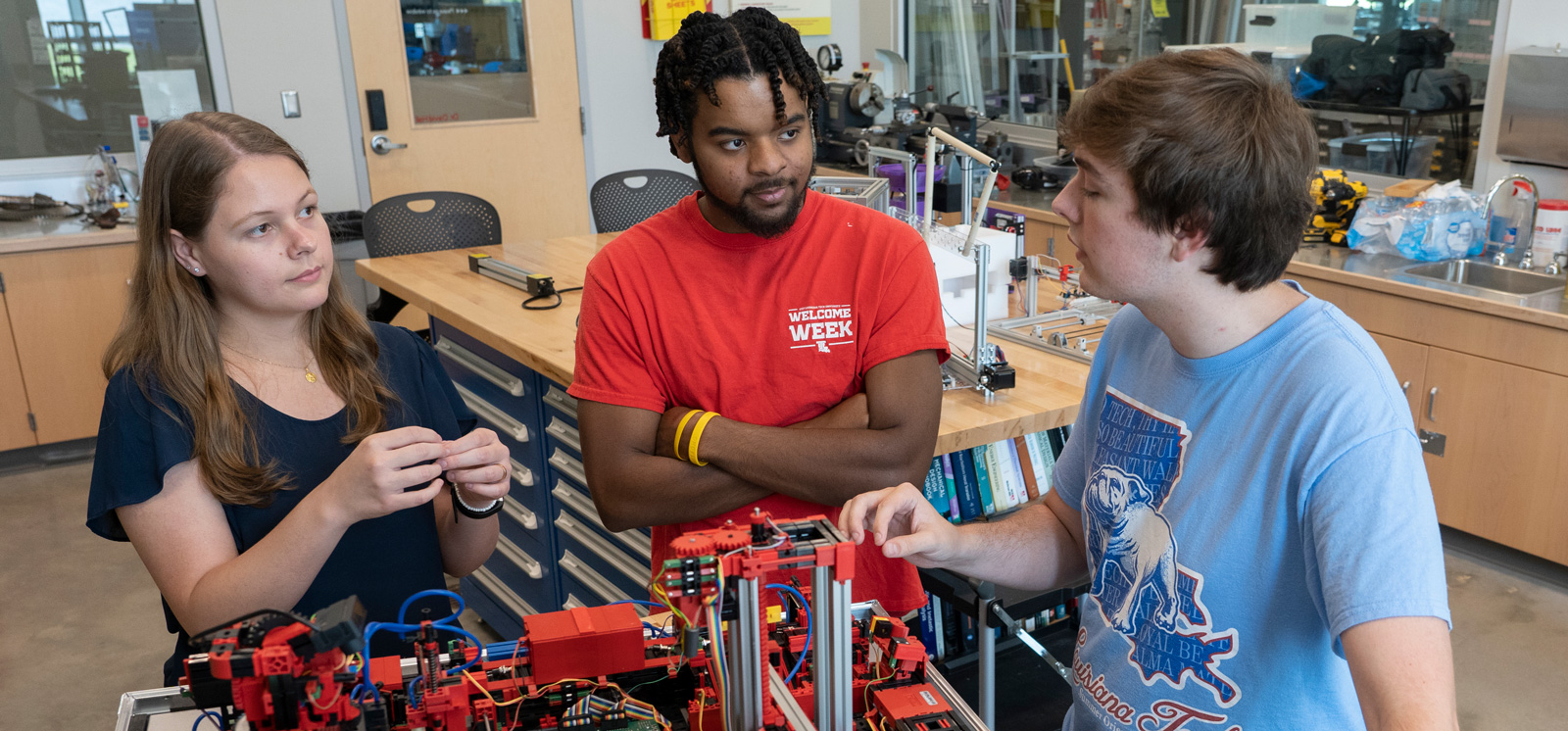
Industrial Engineering
Want to make things work smarter, faster, and better? Louisiana Tech’s Industrial Engineering program prepares you to optimize systems and solve real-world problems across a wide range of industries. You’ll learn how to streamline operations, reduce waste, and improve productivity by combining engineering principles with business strategies.
From manufacturing and logistics to healthcare and tech, industrial engineers are in high demand for their ability to boost efficiency and drive innovation. With hands-on projects, modern tools, and expert faculty, you’ll graduate ready to lead improvements that make a measurable impact wherever your career takes you.
Areas of Study
-
Management Engineering
Combines the technical problem solving of an engineering degree with managerial skills such as organizing and planning. Used to lead teams and optimize the performance in departments to produce an efficient and cost-effective organization. Tools are used to develop, implement, and monitor the process.
-
Human Factors Engineering
Collects data, analyzes, and designs processes that focus on human capabilities and limitations. Looking to minimize risk and optimize safety for workers and users.
-
Manufacturing Engineering
Designs and improves the production of a product through its process in a complex system. Need to stay current with technological advances to produce a high-quality and competitive product.
-
Operations Engineering
Uses mathematical decision-making methods to ensure the operations of a company, like manufacturing or logistics, are optimal.
-
Quality Engineering
Ensures a product or service maintains a high-quality standard by identifying problems, conducting tests, and establishing control methods. Monitors the process over time.
-
Data Engineering
Transforms raw data into a format that can be used for analysis. Finds trends in sets and develops ways for people to access this easily among complex databases.
Certifications
Six Sigma Green Belt
Requirements
Students are required to take the following courses and earn a grade of ‘B’ or higher in each of these courses to complete the requirements of the Six Sigma Green Belt Certification.
Take both of the following courses:
- INEN 400 Engineering Statistics I and
- INEN 401 Engineering Statistics II.
Total: 6 SCH of coursework.
More Information
The cost to take the two required courses is $1,261 per course for a total of $2,522 to complete the Six Sigma Green Belt certification.
Acquiring a greenbelt certificate not only enhances a professional skill set but also improves an individuals’ marketability for obtaining competitive positions with successful organizations and companies. According to Villanova University, “while trained and certified in Six Sigma methodology, a Green belt does not usually practice the methodology full time.” Green Belts can spend up to half of their work time on Six Sigma projects and function as support for Black Belts. They will “use graphs to show process improvement…, create a communication plan to convey accurate information about the project to leadership and other stakeholders, and promote data-driven solutions.”
According to Indeed.com, the largest job website in the world, there are 63,000 jobs related to Lean Six Sigma. Indeed.com states that average Six Sigma Green Belt salaries for job postings nationwide are 42% higher than average salaries for all job postings nationwide. Some examples of jobs are Lean Continuous Improvement Leader, Lean Process Improvement Engineer, Senior Supplier Quality Engineer, Lean Manufacturing Facilitator, etc. The average annual median salary for Six Sigma Green Belts is $95,261.
For more information, contact Beth Hegab.
Six Sigma Black Belt
Requirements
Students are required to earn a grade of ‘B’ or higher in each of the following courses to complete the requirements of the Six Sigma Green Belt Certification.
Take all four of the following courses:
INEN 400: Engineering Statistics I,
INEN 401: Engineering Statistics II,
INEN 403: Design of Experiments for Six Sigma, and
INEN 420: Six Sigma Black Belt Project.
Total: 12 SCH of coursework.
More Information
The cost to take the four required courses is $1,261 per course for a total of $5,044 to complete the Six Sigma Black Belt Certification.
The certified Six Sigma Black Belt is a professional who can explain Six Sigma philosophies and principles, including supporting systems and tools. A Black Belt should demonstrate team leadership, understand team dynamics and assign team member roles and responsibilities. Black Belts have a thorough understanding of all aspects of the DMAIC model in accordance with Six Sigma principles. They have basic knowledge of Lean enterprise concepts, are able to identify non-value-added elements and activities and are able to use specific tools.
According to Indeed.com, the largest job website in the world, there are 63,000 jobs related to Lean Six Sigma. The average annual median salary for Six Sigma Black Belts is $126,551.
For more information, contact Beth Hegab.
Lean Certification
Requirements
Students are required to earn a grade of ‘B’ or higher in the following course to complete the Lean Certification.
- INEN 408: Lean Manufacturing and Management Systems
Total: 3 SCH of coursework
More Information
The cost to take the required course is $1,261 to complete the Lean Certification.
Acquiring a lean certificate validates one’s knowledge and experience with lean principles, enhancing the professional skill set as it interlaces innovative ways of thinking and doing business with real-world applications and results. It also improves an individuals’ marketability for obtaining competitive positions with successful organizations and companies. The lean methodology aims to deliver maximum value while minimizing waste, improving the operations and processes within the organization. When implemented, lean has proven to drive sustainable improvements and results within an organization, accomplishing business objectives.
According to salary.com and indeed.com, “the national average salary for a Certified Lean Specialist in 2019 is $81,574 per year while that of a Certified Lean Manager is $89,032 per year in the United States.”
Indeed.com states that average Lean salaries for job postings nationwide are 42% higher than average salaries for all job postings nationwide. Some examples of jobs are Lean Continuous Improvement Leader, Lean Process Improvement Engineer, Process Improvement Quality Engineer, Lean Manufacturing Facilitator, etc.
For more information, contact Beth Hegab.
Lean Six Sigma Certificate
Requirements
Students are required to complete six courses to earn the Lean Six Sigma Certificate:
1. MATH 241: Calculus I, or MATH 220: Applied Calculus, or MATH 222: Business Calculus;
2. MATH 242: Calculus II or STAT 200: Basic Statistics;
3. INEN 400: Engineering Statistics I or EMGT 414: Statistical Analysis for Six Sigma;
4. INEN 401: Engineering Statistics II or EMGT 466: Six Sigma and Quality Control;
5. INEN 408: Lean Manufacturing and Management Systems or EMGT 411: Theory and Applications of Lean Manufacturing and Management; and
6. INEN 420: Six Sigma Black Belt Project or EMGT 420: Six Sigma Black Belt Project.
Total: 18 SCH of coursework.
Who Should Pursue the Lean Six Sigma Certificate?
The course requirements allow learners from diverse technical backgrounds to earn the Lean Six Sigma with minimal prerequisites. For example, those who have completed all or part of a mathematics, technology or engineering degree may already have the mathematics and statistics requirements. Industrial Engineering Students at Louisiana Tech University can complete the certificate as they complete their undergraduate degree by taking only one additional course (INEN 420).
More Information
The cost to enroll in the six required courses is $1,261 per course for a total of $7,566 to complete the Lean Six Sigma Certification.
Lean Six Sigma is a method that relies on a collaborative team effort to improve performance by systematically removing waste and reducing variation. Lean Six Sigma not only reduces process defects and waste but also provides a framework for overall organizational culture change.
The term Lean is typically used for process/time focused analyses, and Six Sigma is typically more statistical/defect focused. Lean Six Sigma is the best of both sides; it allows you to bring variation in time performance to control and reduce defects with variability-based improvements.
Indeed.com states that the average salary for a Lean Six Sigma Specialist is $110,257 per year in the United States. Some examples of job titles are Lean Engineer, Lean Six Sigma Process Engineer, Quality Manager and Operational Excellence Engineer.
For more information, contact Beth Hegab.
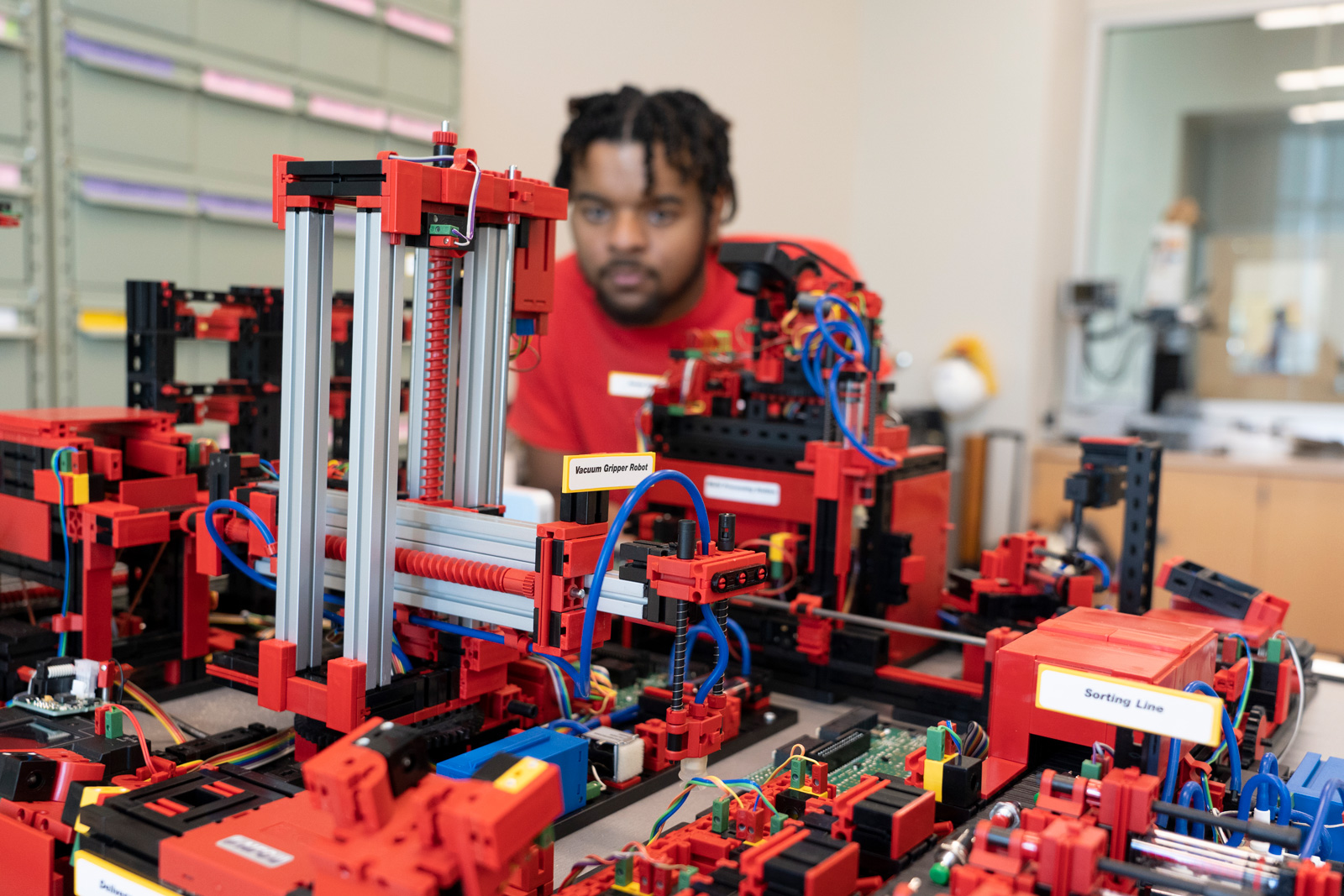
Program Statistics
Average 2022-2023 Starting Salary for Louisiana Tech BS Industrial Engineering Graduates in $
Average 2023 Salary with 10+ Years Experience in Industrial Engineers in the U.S. in $ (According to PayScale.com)
Student-to-Faculty Ratio
%
Percentage of Louisiana Tech Industrial Engineering Graduates Who Recommend the Program
%
Percentage of Louisiana Tech Industrial Engineering Graduates Who Are Happy with the Program
Interested in Joining Our Program?
Whether you’re interested in joining our program or just have questions, we’re here to help.
What is Industrial Engineering?
Industrial Engineering focuses on the optimization of complex processes, systems, and organizations. It combines engineering and business to make informed decisions through interactions with people and the application of industrial engineering fundamentals. Industrial Engineers design and continually improve processes so that they run efficiently with minimal waste or defects. Industrial Engineers focus less on physics-based analysis and design, and more on systems-level analysis of performance. Simply put, industrial engineers make organizations and processes better to improve efficiency and profitability. The Louisiana Tech Industrial Engineering program is accredited by the Engineering Accreditation Commission (EAC) of ABET, https://www.abet.org/. To find out more information about the program mission, educational objectives, student outcomes, and enrollment and graduation data, go to our Accreditation & Enrollment page.
Industrial engineers deal with a number of specialties, including operations research, systems, manufacturing, production, management science, safety, and ergonomics. In this program, you have the opportunity to earn several certifications, two of which are built into the curriculum. At the end of this degree, many students are awarded a Six Sigma Green Belt certification and a Lean Certification by achieving a minimum grade of B in the statistics courses and lean manufacturing & management course. These are industry-recognized quality control programs that utilize process-improvement techniques. You can find out more about them and the optional certifications below.
Percent Increase in Employment Projected 2019-2029
- Industrial Engineers: 12% 83.333%
- Engineers: 4.8% 35%
- Total, All Occupations: 4% 33.333%
Famous Industrial Engineers
Famous Industrial Engineers
Tim Cook (Apple CEO 2011-present)
Chad Holliday (former Chairman and CEO of Dupont 1999-2009; Chairman, Royal Dutch Shell, 2015-present)
William Swanson (Chairman and CEO of Raytheon, 2004-2014)
Mike Duke (President and CEO of Wal-Mart 2009-2013)
Micheal Eskew (Chairman and CEO of UPS 2002-2007)
John Forehand (Accenture, CEO 1999 – 2001, Chairman 2001-2006)
Advising Materials
For a list of prerequisites and required courses, select the curriculum sheets below.
Industrial Engineering Curriculum Fall 2022
Industrial Engineering Curriculum Fall 2019
About Alumni
Below is a list of forty notable job positions of alumni of the Industrial Engineering program from Louisiana Tech. Their positions and industries are marked and show the range of opportunities this degree presents.
Manufacturing Positions | |
---|---|
AT&T Foundation | Planning Engineer |
Baxter Healthcare Corporation | Professional Engineer |
Boeing Co. | Industrial Engineer |
Cameron, a Schlumberger Company | Continuous Improvement Lead |
Cleco | Senior Engineer |
Conoco, Inc. | Production Specialist |
Dow Chemical Company | Site Integration Engineer |
Frito Lay | Industrial Engineer |
GE Oil & Gas | Project Manager |
General Dynamics Corporation | Maintenance Engineer |
General Motors Corporation | Quality Assurance Manager |
Georgia Pacific | Regional Reliability Engineer |
Honda of America Manufacturing | New Model Quality Leader |
Intel Corporation | Technical Program Manager |
Lenovo | Senior IT Systems Engineer |
Lockheed Martin | Industrial Engineer, Simulations |
Neiman Marcus | Industrial Engineer |
Northrop Grumman Ship Systems | Site Manager |
PayPal, Inc. | Systems Engineer |
Schlumberger | Manufacturing Engineer |
Texas Instruments Foundation | Manufacturing Engineer |
The Aerospace Corporation | Senior Project Engineer |
U.S. Department of Defense/US Navy | Industrial Engineer |
Verizon | Network Engineering/Project Manager |
Whirlpool Corporation | Materials Manager |
Nonmanufacturing Positions | |
---|---|
Amazon | Regional Director of Operations |
Campbell Soup Company | Customer Development Lead |
ExxonMobil Foundation – Educational (MG) | Global Project Development |
Johnson & Johnson | Associate Director, External Alliances |
NASA Ames Research Center | Space Biology Manager/Gateway Subsystem Deputy Mgr |
Nibol – Nissan | Brand Manager |
Proctor & Gamble | SUD Launch Leader |
Rockwell Collins | Operations Manager |
Siemens Energy & Automation | Regional Manager |
Target | Operations Manager |
Texas A&M University | Research Scientist |
The J. M. Smucker Company | Packaging Area Leader |
United Space Alliance-NASA Johnson Space Center | NASA Flight Controller |
Healthcare Engineer |
Alumni Testimonials
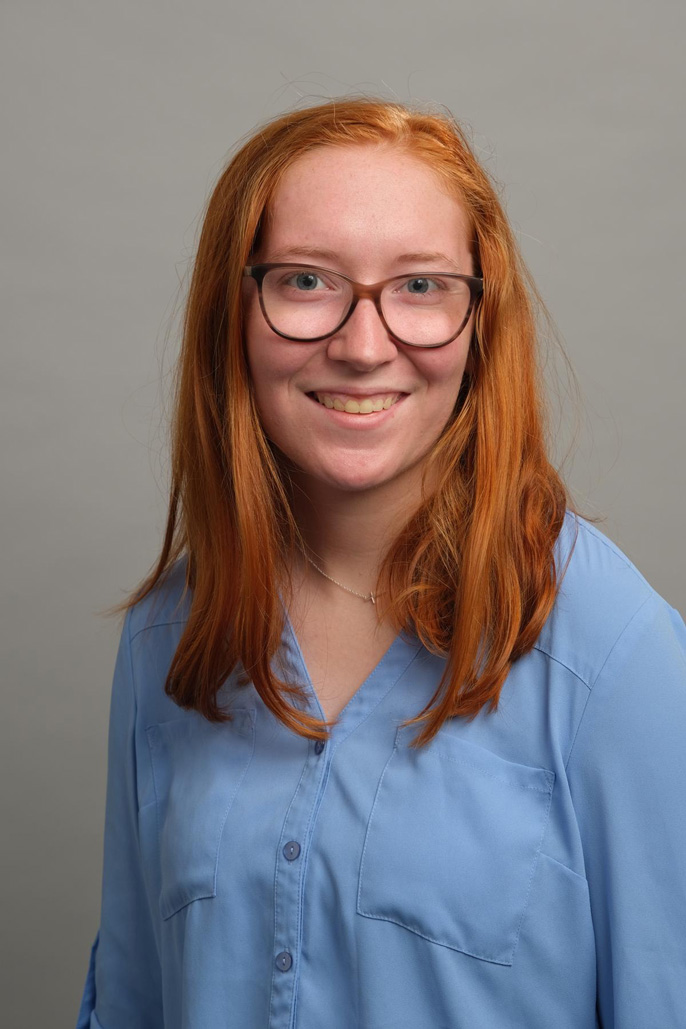
Bethany Williams ’23
“My official role is manufacturing engineering, but I get to use my Six Sigma Black Belt all the time! My second week here, they put me in a Kaizen event, and a month later, I led my own! It was a follow-up to the first one, so the foundation was already there. Now, as the resident black belt, they’re putting me in more Kaizen events. I’m really enjoying my role and considering moving into a process engineering/OPEX role in the future. It’s been really cool getting to use all the skills I learned in your class (and my Green Belt classes) in the real world. It’s also a fun little flex, being one of the only Black Belt-certified engineers in the plant.
“Thanks for starting up the Six Sigma program at Tech. It’s really helped me stand out in the workplace and find something I enjoy doing!”
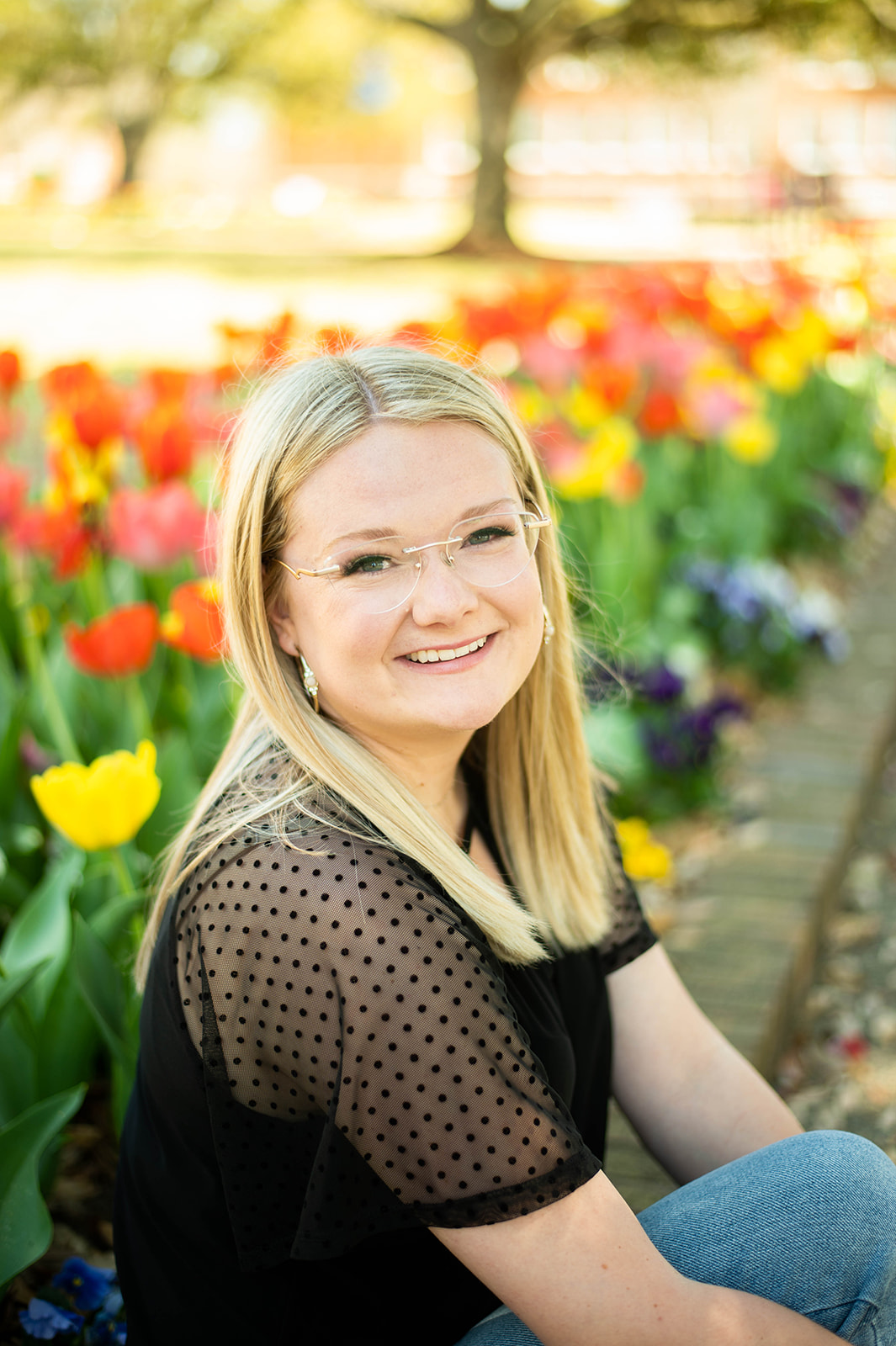
Kambell Rabalais ’22
“One of the biggest takeaways I got from the Industrial Engineering program was that the people in the program really cared about me and my education. My classes always challenged me to think in a new way, learn in a new way, do something new, etc. I got the hands-on experience that you can not get at other schools.
“Now I work for Honda as a New Model Quality Engineer, and I am grateful for everything I learned while in school, even the things I don’t apply directly to my position. Thanks to my experiences at Louisiana Tech, new things don’t intimidate me as they would have before.
“If you can do one thing while you’re in school, appreciate the people around you and absorb all the knowledge you can. Industrial Engineering is a large field, and you never know what skills you will be applying in your job!”
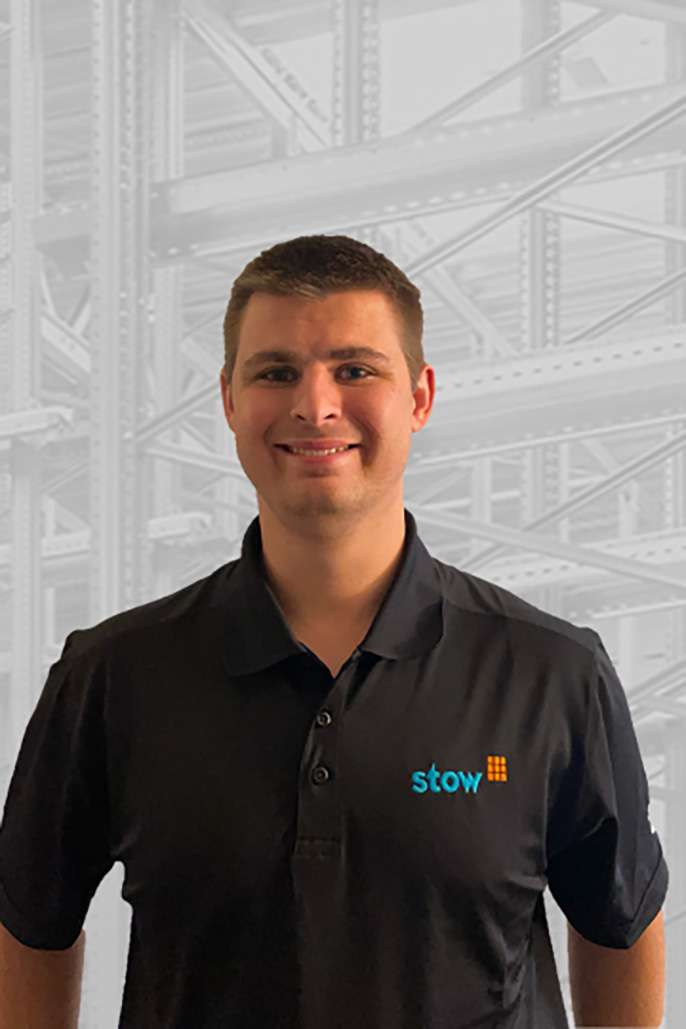
Noah Phenice ’21
“As a recent alum of Louisiana Tech’s Industrial Engineering program, I have the opportunity to look back and truly value my education. Since graduating, I have had the chance to join the materials handling industry (currently as a solution development engineer), travel the world for work, and pursue my education further; all opportunities which arose from successfully completing this program.
“And while there are many industrial engineering programs in the country, Tech’s is not only highly accredited but has one of the highest returns on investment compared to other programs and universities. However, the true reason I chose Louisiana Tech’s Industrial Engineering program is because of its unique hands-on / project-based curriculum. This approach is for people who not only want to learn theory but also how to apply it. It is for people who love to learn, solve challenging problems, and are willing to work hard to build a foundation that will support them for the rest of their professional careers. I’ve made many decisions, but none were greater than deciding to join this program.”
Current Student Interviews
Noah Phenice, Senior ’21
What made you interested in choosing Industrial Engineering as your major?
Learning what an industrial engineer actually does was the first thing for me to consider before switching programs. Compared to other engineering disciplines, industrial engineers have by far the most flexible career paths and have courses that uniquely combine concepts from both engineering and business.
What have you enjoyed most about the Industrial Engineering program?
My favorite part of the industrial engineering program is the senior design project. This project allows us to partner with a company and uniquely apply all of the techniques and concepts we’ve learned.
What do you want to do in the future with what you’ve learned?
In the future, I hope to make a significant impact on whichever company I have the opportunity to work with. Whether it’s improving productivity, quality, or efficiency, I plan to prove the value that industrial engineers can provide to any process.
What advice do you have for incoming Industrial Engineering students?
My advice to incoming Industrial Engineering students would be to take full advantage of your opportunities while being a student at Tech. Although working towards a career is the most important goal, the way to stand out is by serving and supporting your university in whatever way you can. Whether it’s attending athletic events, helping an organization, or serving as a student worker, make the most of the limited time you have as a student.
Alexander Brodtman, Senior ’21
What made you interested in choosing Industrial Engineering as your major?
When I started at Tech in 2016, I was actually a student in the college of business. I became interested in engineering because I saw the projects my friends worked on throughout the 120 series and their coursework seemed much more interesting and useful than mine. After completing the 120 series, it was clear to me that coding, circuits, and batch problems were not my strong suits. I was unsure about which engineering discipline was best for me, so I decided to talk to students who were further along in their curriculums than I was. This was the first time I learned about Industrial Engineering as an option. It took some time for me to settle on IE as my major, but after doing some research on the courses in the curriculum I made the switch and have not looked back. Thanks to the great professors in the IE department and guidance from students who came before me, I will be graduating on time this spring with a degree I never thought I would have had five years ago.
What have you enjoyed most about the Industrial Engineering program?
There are a few things I love about our Industrial Engineering program. First and foremost, I think that every class I have taken under the INEN label has offered knowledge that will be useful once I graduate. From economics to lean manufacturing, everything I have learned can be applied to everyday problems both inside and outside the workplace. Another benefit of the Industrial Engineering program is the size of the classes. Small class sizes make learning more personable and having the same group of students in most of your classes from quarter-to-quarter makes project work much simpler. Lastly, the professors in the IE program are top-notch. Every industrial engineering professor I have encountered wants their students to succeed and are willing to help in any way that they can.
What do you want to do in the future with what you’ve learned?
I plan on starting a career in manufacturing once I graduate. I hope to earn a position in a continuous improvement role where I can focus on learning more about Lean Six Sigma applications in a production setting. Eventually, I plan to move into a management position and possibly work toward my Master Black Belt Certification. Fortunately, I know that if I do not find an ideal position right after graduating I have learned a valuable set of skills that will make me a valuable asset wherever I go.
What advice do you have for incoming Industrial Engineering students?
My advice to incoming IE students is to stick with it. No matter what engineering discipline you start with, some of the most difficult quarters you will have will be at the beginning of your academic career. An engineering degree is not easy to attain, but not many things that are worth having are. I would also suggest that you thoroughly explore each discipline, do not make up your mind on which discipline you want to major in right away. The 120 series does an excellent job of introducing you to most of your options but talking with older students or professors about their experiences can give even more insight.
Claire Dorsett, Senior ’21
What made you interested in choosing Industrial Engineering as your major?
I always loved mathematics and statistics, which pointed me to the engineering field in general. I was introduced to Industrial Engineering my first quarter at Louisiana Tech, but it wasn’t until my sophomore year that I realized the description fit exactly what I knew I enjoyed doing. I have a love for problem-solving, which I believe crops up in industrial engineering more than most other engineering fields, as you analyze an already existing process specifically for problems or issues that could (or do) occur. To me, looking at the fine details of an already built process and using mathematics and statistics to improve it is both challenging and interesting. Being a bit of a perfectionist also helps!
What have you enjoyed most about the Industrial Engineering program?
Having the opportunity to work on realistic projects at Louisiana Tech has been both interesting and informative. I believe it has given me a very realistic view of the kind of work I will do once I enter the workforce. The Six Sigma Black Belt and Lean Six Sigma certification programs were also great opportunities that allowed me to get a jump on learning the various applications of Six Sigma and Lean improvement tools.
What do you want to do in the future with what you’ve learned?
I believe that there are so many companies in the world that are not doing things as efficiently as they could be. I would love to be a part of Six Sigma projects for improving companies and processes that already exist, especially if I would be able to increase sustainability (environmentally speaking). Specifically, I would want to be a statistics consultant on these projects, as statistical analysis is where I find myself the most beneficial contributor to a project group.
What advice do you have for incoming Industrial Engineering students?
If you want to have an opportunity to work in any type of company, doing analysis of a process, diagnosing a problem, or saving money through efficiency, Industrial Engineering is the way to go, and you are in the right place. It touches not only on every engineering discipline but also on financial and human resource aspects that are applicable to any and every company or field that you could possibly want to work in. A little tip: teamwork really is at the heart of engineering. Reach out to your professors and peers! Everyone in this program is ready and willing to help you every step of the way.
Faculty
Associate Dean of Undergraduate Studies, Academic Director of Instrumentation and Control Systems Engineering Technology and Industrial Engineering, Associate Professor of Biomedical Engineering
Departments: Biomedical Engineering, Center for Biomedical Engineering and Rehabilitation Sciences, Industrial Engineering, Instrumentation and Control Systems Engineering Technology, Molecular Science and Nanotechnology
Senior Lecturer, Industrial Engineering; Senior Lecturer, Engineering Technology and Management; Master’s Coordinator, Engineering and Technology Management
Departments: Engineering and Technology Management, Industrial Engineering, MALT Center
Lecturer
Departments: Civil Engineering, Industrial Engineering, Trenchless Technology Center
Program Chair, Professor, Associate Director MALT Center
Departments: Engineering and Technology Management, Industrial Engineering, MALT Center
Visiting Lecturer
Departments: Industrial Engineering, Instrumentation and Control Systems Engineering Technology
Project Based Learning Specialist
Departments: Engineering and Technology Management, Industrial Engineering, Instrumentation and Control Systems Engineering Technology
Advisory Board
About the Industrial Engineering Advisory Council
The Louisiana Tech University Industrial Engineering Advisory Council was established in the summer of 2001. The Industrial Engineering Program Chair is an ex-officio member and the secretary of the IEAC. The IIE Student Chapter President is also an ex-officio member of the IEAC and attends the IEAC meeting.
The purposes of the Industrial Engineering Advisory Council, as noted in its constitution, are:
1. To provide counsel on educational activities and enhancement.
2. To provide counsel on research directions.
3. To facilitate communication between the program and industry, alumni, and government.
4. To provide liaison with the Engineering and Science Foundation.
5. To provide a forum for undergraduate and graduate students to interface with industry representatives to gain exposure to a broad spectrum of industry not in the recruiting role.
6. To assess the effectiveness of the recommendations made to the program by the Council and in the abilities of graduates to achieve the program educational objectives and student outcomes.
Advisory Council Roster (as of June 2021)
Craig Caskey (BSIE 2009)
Continuous Improvement Manager
Alliance Compressors
Craig.Caskey@Emerson.com
Term Expires: Spring 2022
Jade Shepard (BSIE 2013)
Manufacturing Engineer
MECO- Mechanical Equipment Company
jdshepard@meco.com
Term Expires: Spring 2022
Ryan Grumble (BSIE 2012)
Operations Industrial Engineer, Southern Area
US Postal Service
ryan.a.grumble@usps.gov
Term Expires: Spring 2022
Nwadiuto Adebamiji (BSIE 2015)
President and CEO
PP EXT 01, LLC
nwadi.ade@gmail.com
Term Expires: Spring 2023
Mark Taylor (BSIE 2015)
Project Manager
PumpWorks 610/DXPE
marktaylor@pumpworks610.com
Term Expires: Spring 2024
John Garrison (BSIE 2002)
Advanced Manufacturing Training Director
Louisiana Delta Community College
johngarrison57@yahoo.com, johngarrison1@ladelta.edu
Term Expires: Spring 2022
Gauge T. Means (BSIE 2015)
UNFI
Gaugemeans@gmail.com
Term Expires: Spring 2022
Adam F. Parker (BSIE 2016)
Operations Engineer Sr.
Lockheed Martin Missiles and Fire Control
adam.f.parker@lmco.com
Term Expires: Spring 2022
Mary Peyton Payne (BSIE 2016)
Industrial Engineer
FA18 Super Hornets, Boeing
Mary.P.Payne@boeing.com
Term Expires: Spring 2023
Janelle Cooper (BSIE 2014)
Hydrocarbons Supply Chain
LA Site Integration Mgr & Feedstocks Planner Dow Hydrocarbons and Resources, LLC
jcooper2@dow.com
Term Expires: Spring 2023
John Davis (BSIE 2017)
Operations Industrial Engineer
Montgomery Processing & Distribution Center, US Postal Service
John.m.davis2@usps.gov
Term Expires: Spring 2023
Sari Freeman (BSIE 2017)
Delivery Manager II Fujitsu Network Communications
sari.freeman@yahoo.com, sari.freeman@fujitsu.com
Term Expires: Spring 2024
Concurrent Enrollment
If you have a 3.2 GPA or higher and are within 30 semester credit hours of finishing your degree, you can take up to 12 graduate semester hours during your undergraduate degree and get both graduate and undergraduate credit. Below is a list of the eight INEN classes you can take at the graduate level that will count for both.
- INEN 400: Engineering Statistics I or INEN 514: Statistical Analysis of Six Sigma
- INEN 401: Engineering Statistics II or INEN 566: Six Sigma and Quality Control
- INEN 403: Design of Experiments for Six Sigma or STAT 507: Design and Analysis of Experiments
- INEN 420: Six Sigma Black Belt Project or INEN 520: Six Sigma Black Belt Project
- INEN 407: Simulation or INEN 504: Systems Simulation
- INEN 408: Lean manufacturing and Management Systems or INEN 511: Theory & Applications of Lean Manufacturing and Management
- INEN 410: Manufacturing Systems Management or INEN 505: Manufacturing and Operations Analysis
- INEN 416: Project Management or EMGT 518: Project Management
For information about the qualifications and how to apply go to https://coes.latech.edu/graduate-programs/concurrent-enrollment/ or contact your advisor.