COLLEGE OF ENGINEERING & SCIENCE
Unit Operation Labs
Chemical engineering students at Louisiana Tech learn that safety is the highest priority at the Chemical Engineering Laboratory. The Chemical Engineering Laboratory is an open bay, two-story 3,400 square foot work area dedicated to chemical engineering. Students work in small teams and with the lab instructor when in the laboratory (small class sizes allow for one-on-one interaction with the students).
We have a real-world focus with a hands-on application of the unit operations students learn in the classrooms. Lab experiments deal with evaporation, heat exchangers of various types, absorption, distillation, drying, reactors, fluid flow, pumping systems, fermentation, pulp and paper and process control. Before graduation, each student will have completed 13 unit operations based experiments plus the process control lab.
Lab reports help prepare the students for effective communication to their peers and managers. The lab compliments intern experiences and helps prepare the chemical engineers for their positions in chemical engineering industries
Junior Lab Equipment
Pulp and Paper Experiment
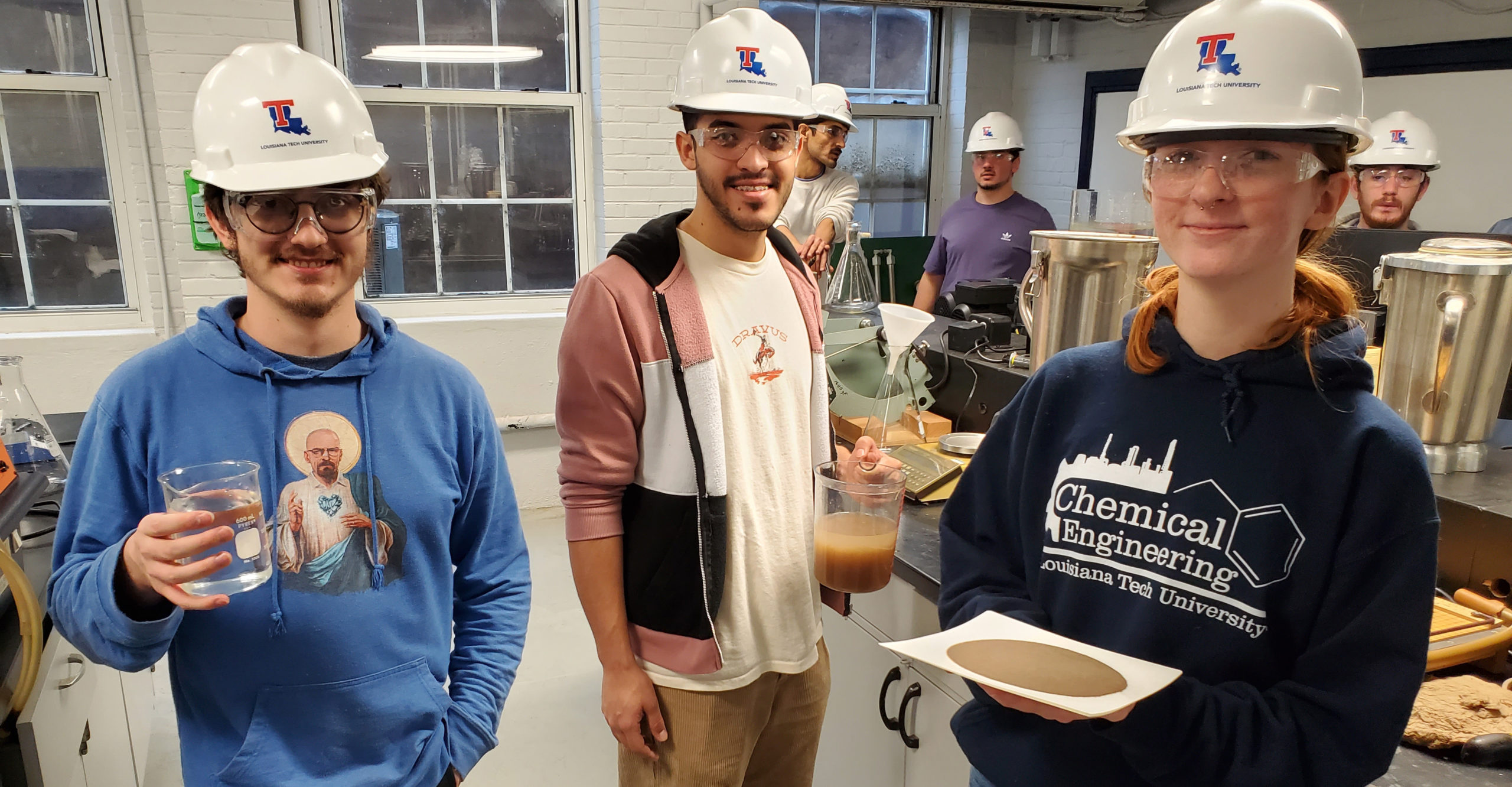
We start with dried pulp and mix that in water in an industrial blender, the amount of pulp along with the time and intensity of the mixing helps determine the paper’s properties. We form the three sheets of paper (with varying paper properties) then dry them in in a quick dryer system. Once the paper is dried, we test for the properties of the paper with a Tear Test and a Freeness Test. This is the same equipment a Louisiana Tech Engineer would see in a Paper Mill.
Cooling Tower
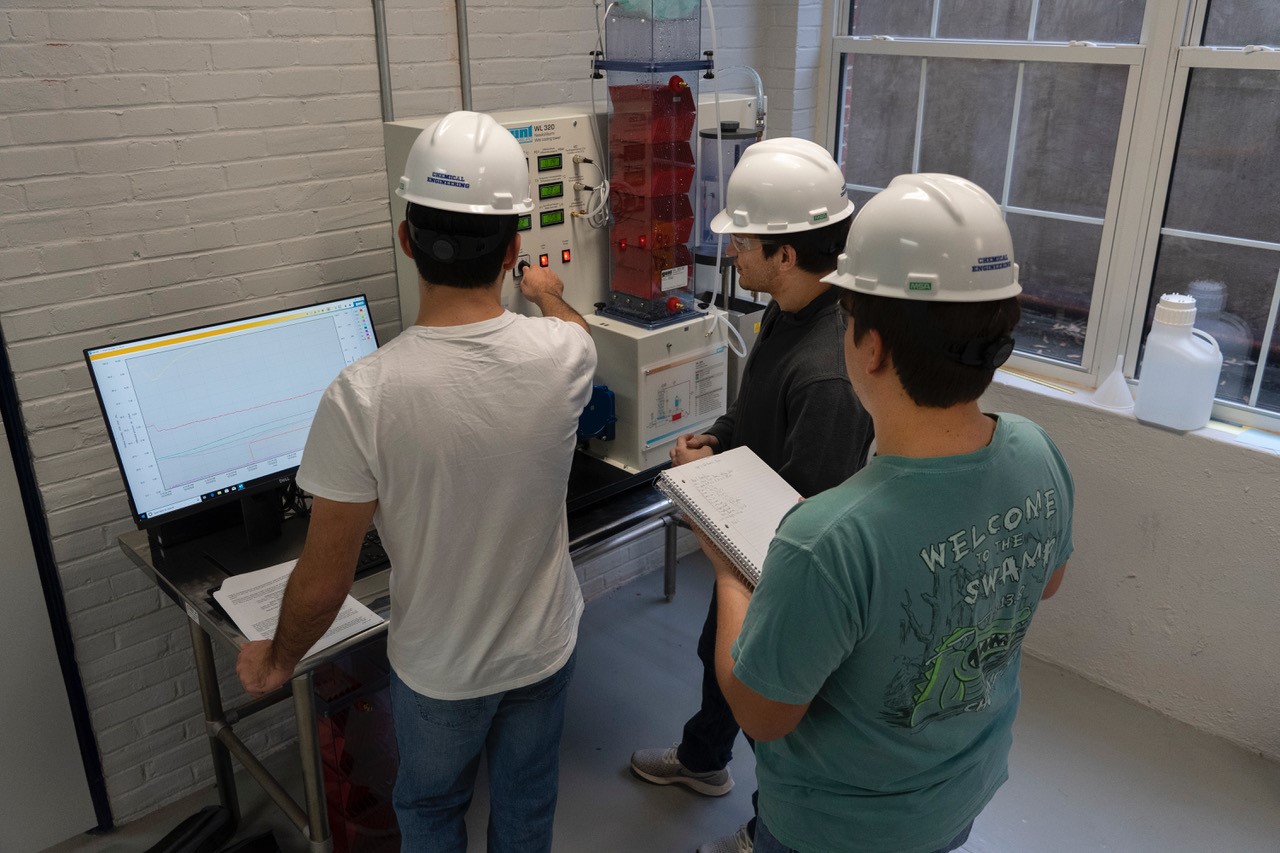
Cooling towers are used throughout chemical engineering industries to remove heat from the processes. Typically, a cooling fluid (water) is pumped from the cooling tower into the plant and through heat exchangers to remove heat from unit operations such as condensing steam, cooling a reactor, cooling for a refrigeration unit, etc. The students cool a recirculated water stream with a heat load simulating the processes being cooled. Various characteristics are changed during the experiment such as airflow rate, water flow rate, air temperature, etc. The students collect the data and develop mass and energy balances around the cooling tower.
Distillation Column (Glass)
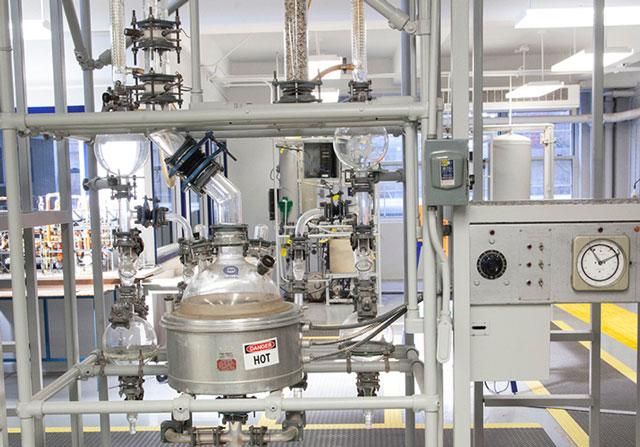
The distillation column is one of the most common liquid-liquid separation systems used in chemical engineering industries. Distillation can be used to separate binary or multi-component mixtures. This column is made of glass so you can see the condensing liquids on the trays. We separate an isopropanol/water solution in this column. The students use their data to plot concentration versus tray number, predict separation using the McCabe-Thiele method and determine tower efficiency.
Falling Ball Viscometer
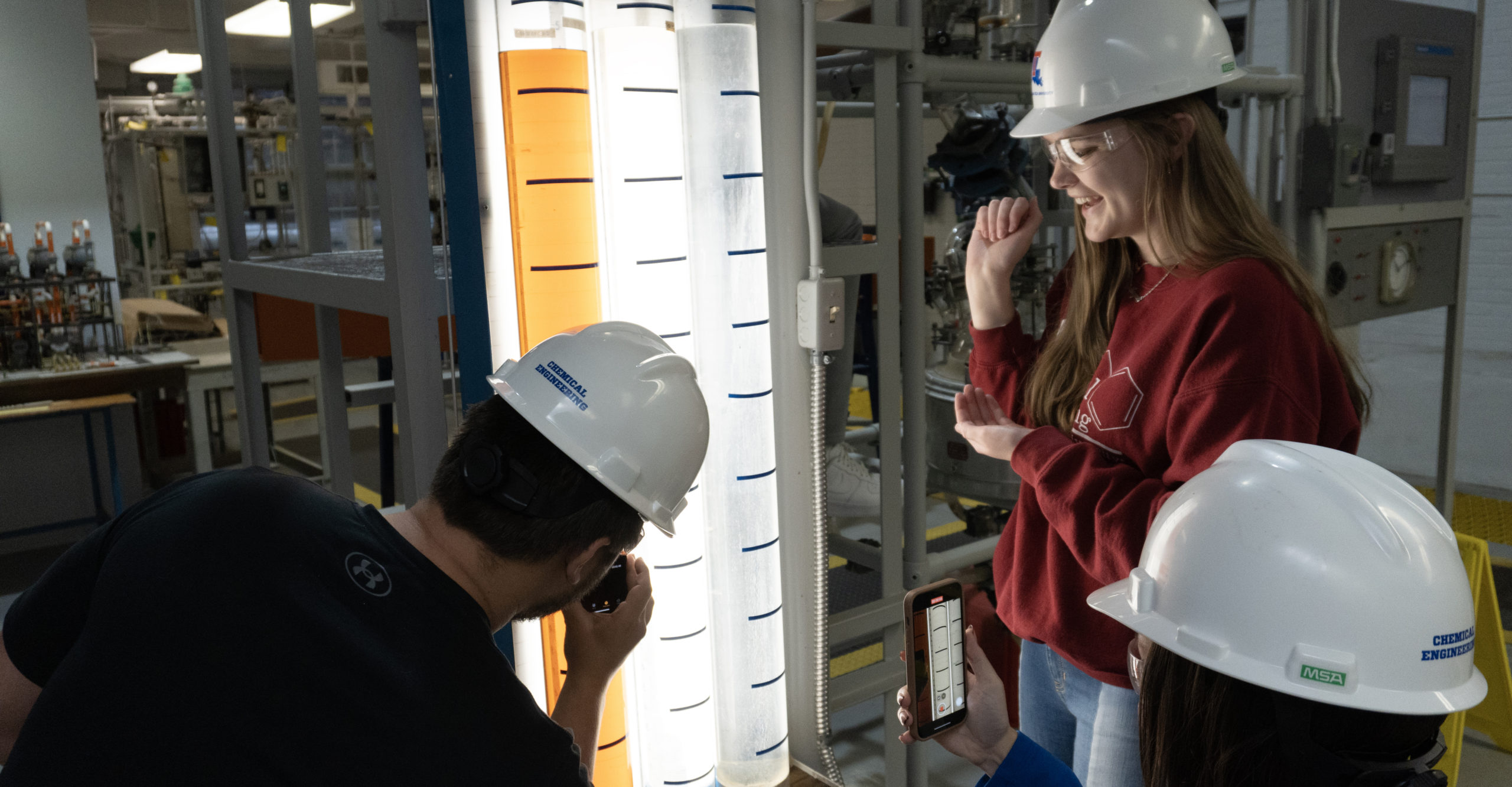
The falling ball viscometer system helps the students determine the viscosity of three different liquids (water, glycerin, and oil). Several small spheres of different sizes and densities are timed as they drop through each fluid. The data obtained is then used by the students to determine fluid viscosity. The experiment is done as a team but the pre-lab and post-lab reports are done individually (just for this experiment).
Heat Exchangers (Benchtop)
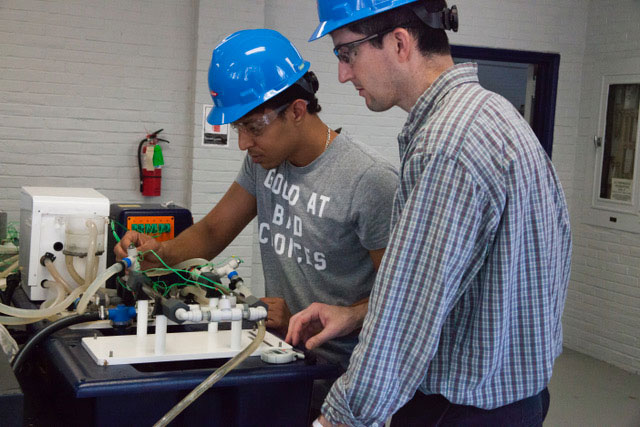
A heat exchanger is a device typically used to transfer heat (energy) between two fluids. These fluids are usually separated by a solid wall to prevent mixing. We have a double pipe, shell and tube, and plate and frame heat exchangers for our benchtop experiments. Circulated hot water heats the cool tap water in the system. The students perform energy balances and determine heat transfer coefficients.
Pressure Loss in Piping Network System
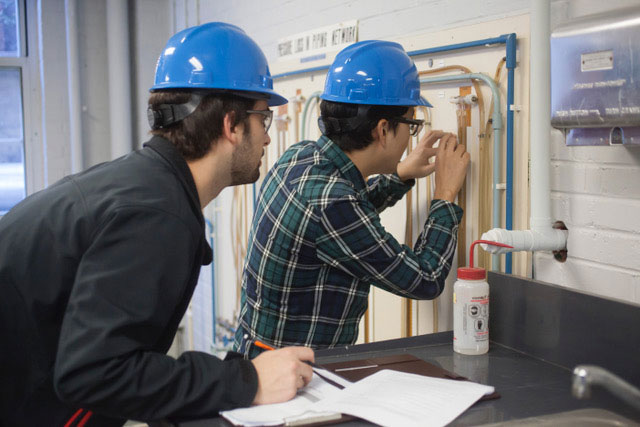
The pressure loss in the piping network system (also called the fluid flow system) demonstrates the pressure drop (energy loss) of a fluid traveling through a piping network. Pressure loss occurs in straight run piping as well as through various obstacles (elbows, sudden expansions/contractions, etc.). Students measure these pressure drops and compare these to the pressure drops predicted by Bernoulli’s equation.
Series and Parallel Pumps
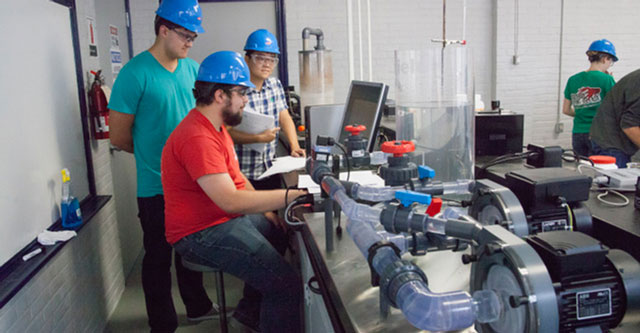
The series and parallel pump system provides hands-on knowledge of how pump systems work. The system provides a way to collect head and flow rate data for a pair of centrifugal pumps in operation, allowing students to create pump curves. Students can then compare these pump curves to theoretical predictions in several scenarios (single pump, varying speed, series flow, parallel flow, etc.).
Tray Dryer
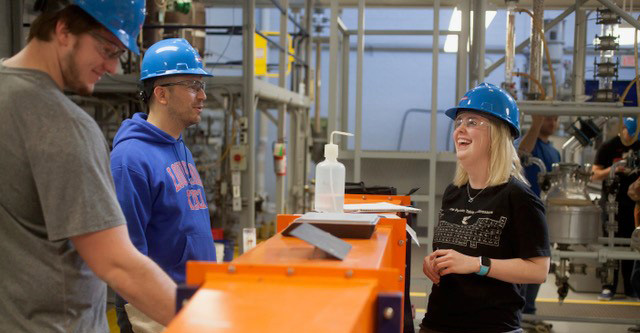
The tray dryer is a horizontal chamber with removable trays in the center area. A fan and heater are located at the air feed end, where the air temperature and speed are controlled. Air passes over the trays, drying the material on them. The students determine drying rates at equilibrium conditions, use wet and dry bulb thermometers, use a psychometric chart and do a mass balance for water in the system.
Senior Lab Equipment
Fermentation (Bio-chemical Reactions)
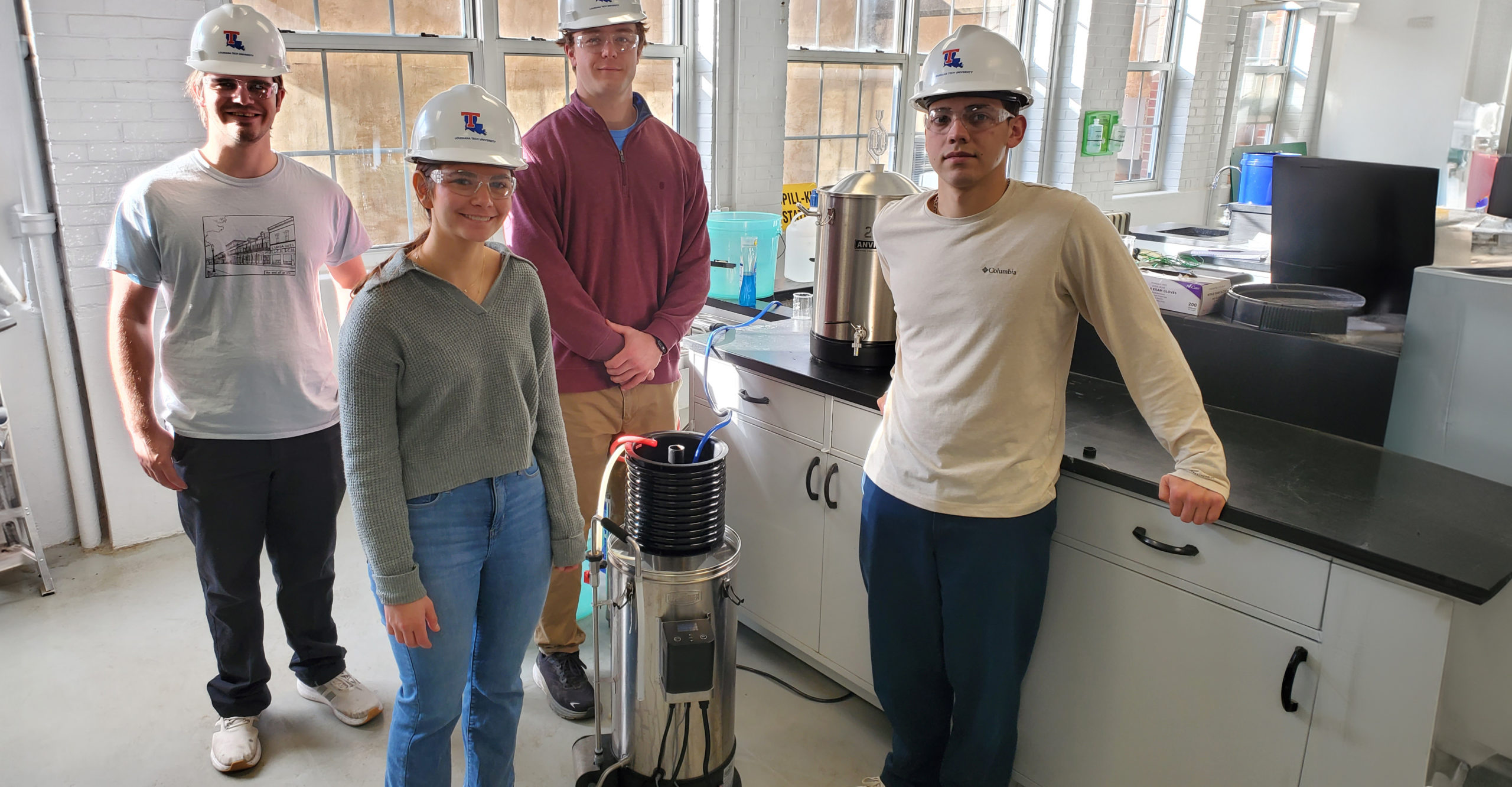
One of the student’s favorite experiments is Brewing Beer. We start with grain and Hops. Mill the grain and use an all in one Grainfather Brewing System to go through the brewing process. After the initial brewing is complete, the material is put in a Fermentation Vessel and left to react for a week. When the students return, they measure the properties of the Beer (including alcohol content). Sorry, they do not get to taste the Beer.
Absorption Column
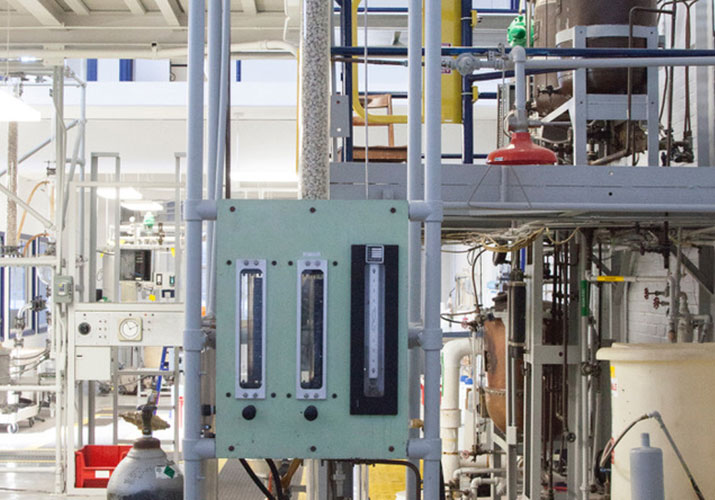
An absorption column is used to separate out components of a rising gas with the use of a falling liquid to adsorb or react with a component(s) of the gas. In our absorption tower, the gas goes in at the bottom of the tower. It, along with any impurities it contains, begins to flow to the top. As it moves toward the top, the liquid is sprayed into the tower wetting the packing material. The wet surfaces and droplets catch impurities in the gas and carry them to the bottom of the tower for collection. Students experimentally determine the concentration of the transferred solute in this liquid and compare this data to predictions based on mass transfer theoretical value and also to the solubility limit.
Distillation Column (Large)
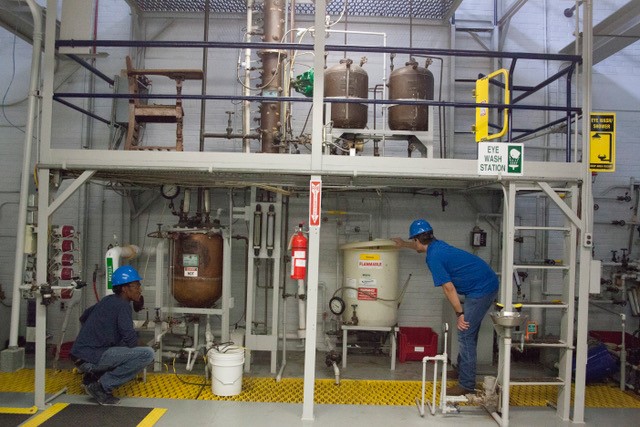
The distillation column is one of the most common liquid-liquid separation systems used in chemical engineering industries. Distillation can be used to separate binary or multi-component mixtures. The students separate isopropanol from normal propanol in this two-story column. Students use the steady-state data obtained to calculate the re-boiler and condenser duties. They plot the steady-state temperature profile in the column and estimate the corresponding composition profile in the column. They create a McCabe-Thiele diagram for this system and compare the theoretical number of trays needed for this separation to the actual number needed to estimate the overall tray efficiency.
Double Effect Evaporator
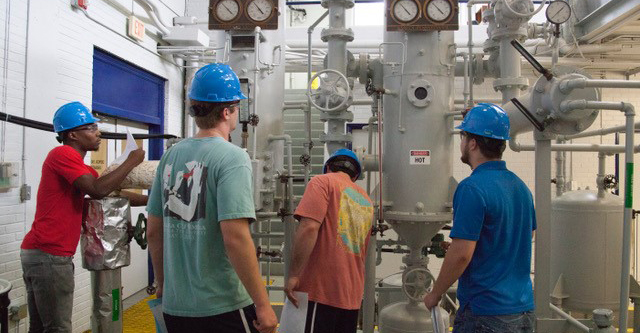
The double effect evaporator separates the feed stream into distilled and concentrated streams. The generated steam is used to further concentrate the liquid stream. The reuse of the steam gives the cost savings value to this technology. Students run the system batch and continuous modes. Students will perform mass and energy balances for the system based on the data they obtain. The students also develop a theoretical model of the system to compare to the actual data.
Heat Exchangers (Large)
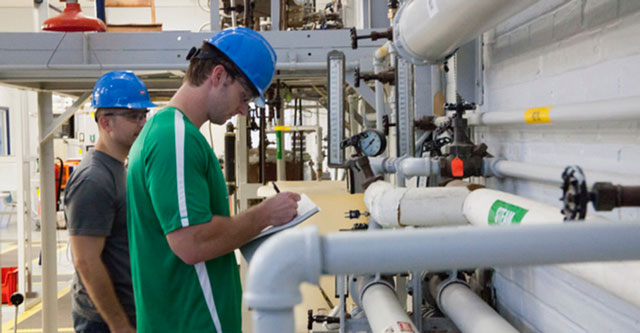
A heat exchanger is a device typically used to transfer heat (energy) between two fluids. These fluids are usually separated by a solid wall to prevent mixing. There are three large heat exchangers on the lab wall; two are double-pipe exchangers (each of a different length) and one is a shell and tube. Steam heats the oil in the system then water cools the oil. The students perform energy balances to determine the heat transfer coefficients and the surface area based on the data they obtain. They use this data to determine if either of the double pipe heat exchangers have fins on the inner pipe.
Tubular Reactor
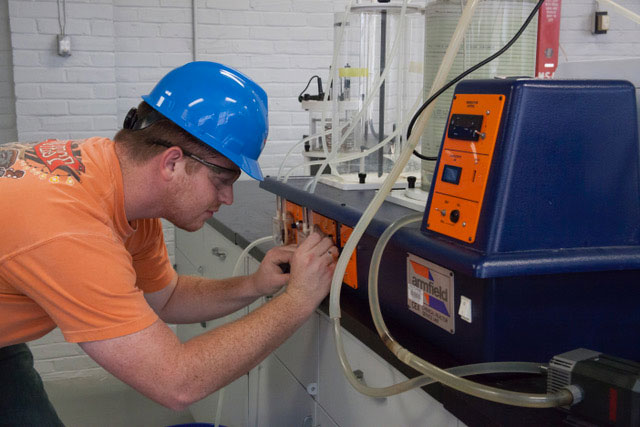
The tubular reactor is used to react ethyl acetate with sodium hydroxide producing ethanol and sodium acetate. The feed materials flow into the tubular reactor where the solution is maintained at a constant temperature. Conversion is measured by an in-line conductivity meter. An optional Continuously Stirred Reactor is also available. The students determine the effect of dissimilar reagent flow rates and the effect of temperature on the reaction kinetics.
Process Control Systems Equipment
Process Control Systems
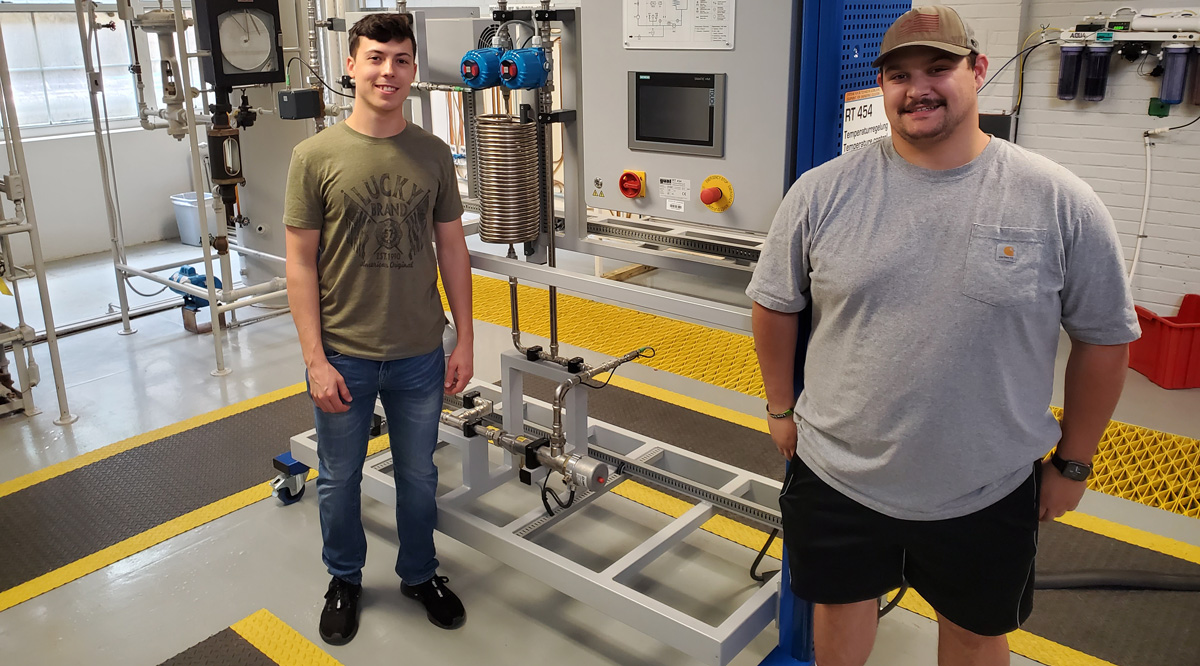
The process control experiment shows the different dynamics between level, flow and temperature control. The Level Control System is connected to a computer in the Process Control Lab. Control characteristics such as the proportional, integral, and derivative values (PID) are programmed into the system and control dynamics are recorded for calculations. The completely pneumatic Flow Control System used by the students to demonstrate the proportional and integral (PI) value impact on flow control. The Temperature Control System shows the different dynamics of PID control for temperature compared to level control.